Hello! Thank you for anyone who is reading/replying, This forum has been a hugely helpful, but the more I read the more I feel like I have questions... hopefully my homework has taken me half-way.
Background
My wife and I recently bought our first home together. Having an environment for me to make music was an essential requirement. The house we bought has a detatched garage, which will be turned into my studio.
I appreciate there are limits to what I'll be able to achieve with this space, but I'm very excited to have a dedicated writing room, I never had this before.
Garage Specs (in cm)
I have posted a few pictures including a floor plan. Below is a bit more detail:
Room size: 310 x 520 x 250 (to the wooden beams - actual ceiling goes higher)
Garage door: 252 wide
The side doors 45 from the wall, and 84 x 193
Pillars on the long sides: 11 (sticking out) x 44 (length)
The workbenches and sink on the side are being removed
Garage Roller Door
Possibly the first thing to think about: the garage door. Either I do a great job at insulating it or I have the door removed with a wall being erected in its place. The latter is more expensive and I need to get builders in... but maybe it's worth it?
Roof
The roof is a also a concern. I'm assuming I need to look into insulating it, but I fear it will be tricky. The beams seem strong, I was hoping to put some panels resting on top of the beams, and insulating wool resting on the panels. I wonder if the actual wooden beams sticking out (at about 2.5m from the floor) will give any problems?
Soundproofing
I found conflicting information about how much of the walls need to be covered to soundproof the garage. Some sites suggest every last inch needs to be covered in insulation, others suggest strategically placing acoustic panels on ~30% of the room will do the job. I'm currently planning on building a full "room within the room" (genieclip + stud wall), is this considered a good approach?
Pillars
About half-way through the room there's pillars slightly sticking out (11cm) from the walls. I understand corners/irregularities need to be managed. Is it enough to add acoustic panels to the adjacent bits of wall, to even out those 11cm? This will leave that small section of the wall slightly less soundproofed.
Door
The small door on the side will be my only way to access the studio. I plan on obtaining a soundproof door, although the size of the existing door seems to be non-standard so it might be tricky. Any advice on this?
Floor
The floor is currently concrete. Some studios have carpets to reduce the sound reflections, is that southing I need to consider at this stage or can I wait until later stages of the studio development?
Acoustic Treatment
I also appreciate that soundproofing and acoustic treatment are two related but separate topics... at the moment I'm focusing on the former, fully aware I will need to take great care of the latter. Any tricks I might be missing by compartmentalising the two too much?
Thank you to anyone who provides any insights!
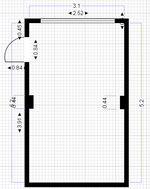
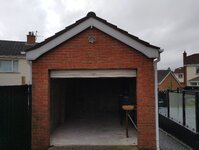
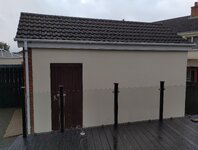
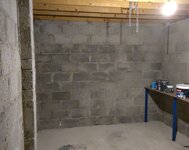
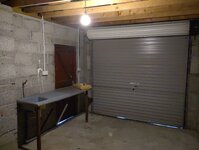
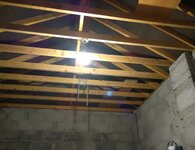
Background
My wife and I recently bought our first home together. Having an environment for me to make music was an essential requirement. The house we bought has a detatched garage, which will be turned into my studio.
I appreciate there are limits to what I'll be able to achieve with this space, but I'm very excited to have a dedicated writing room, I never had this before.
Garage Specs (in cm)
I have posted a few pictures including a floor plan. Below is a bit more detail:
Room size: 310 x 520 x 250 (to the wooden beams - actual ceiling goes higher)
Garage door: 252 wide
The side doors 45 from the wall, and 84 x 193
Pillars on the long sides: 11 (sticking out) x 44 (length)
The workbenches and sink on the side are being removed
Garage Roller Door
Possibly the first thing to think about: the garage door. Either I do a great job at insulating it or I have the door removed with a wall being erected in its place. The latter is more expensive and I need to get builders in... but maybe it's worth it?
Roof
The roof is a also a concern. I'm assuming I need to look into insulating it, but I fear it will be tricky. The beams seem strong, I was hoping to put some panels resting on top of the beams, and insulating wool resting on the panels. I wonder if the actual wooden beams sticking out (at about 2.5m from the floor) will give any problems?
Soundproofing
I found conflicting information about how much of the walls need to be covered to soundproof the garage. Some sites suggest every last inch needs to be covered in insulation, others suggest strategically placing acoustic panels on ~30% of the room will do the job. I'm currently planning on building a full "room within the room" (genieclip + stud wall), is this considered a good approach?
Pillars
About half-way through the room there's pillars slightly sticking out (11cm) from the walls. I understand corners/irregularities need to be managed. Is it enough to add acoustic panels to the adjacent bits of wall, to even out those 11cm? This will leave that small section of the wall slightly less soundproofed.
Door
The small door on the side will be my only way to access the studio. I plan on obtaining a soundproof door, although the size of the existing door seems to be non-standard so it might be tricky. Any advice on this?
Floor
The floor is currently concrete. Some studios have carpets to reduce the sound reflections, is that southing I need to consider at this stage or can I wait until later stages of the studio development?
Acoustic Treatment
I also appreciate that soundproofing and acoustic treatment are two related but separate topics... at the moment I'm focusing on the former, fully aware I will need to take great care of the latter. Any tricks I might be missing by compartmentalising the two too much?
Thank you to anyone who provides any insights!
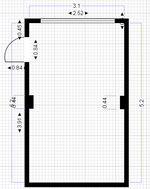
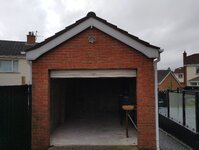
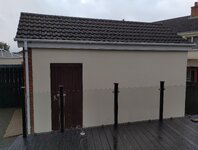
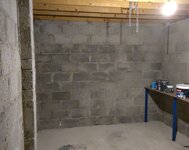
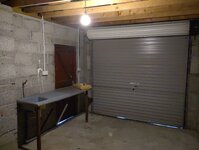
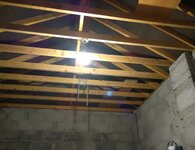